反应堆压力容器是通过不锈钢管道与外设备,如主泵、蒸发器与稳压器等连接,见图8-7。
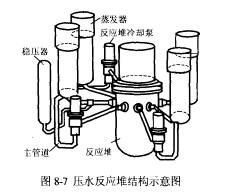
因此,不锈钢管道焊缝的检验也是核设施检验的重点之—。由于奥氏体不锈钢焊缝结晶方向性强,声学性能各向不同,因而促使其声速与声衰各向异性。奥氏体焊缝粗大组织会引起较高的噪声信号,容易形成伪缺陷。这些因素给超声检测不锈钢管道焊缝带来了很大困难。
在PISC-Ⅲ循环试验项目中,对锻造不锈钢管道、锻造与铸造不锈钢管道和铸造与铸造不锈钢管道之间的奥氏体焊缝分别进了超声检测试验。其中所制造的各类试件、焊缝与缺陷专参数见表8-4,

参加者采用的超声检测技术与参数见表8-5。
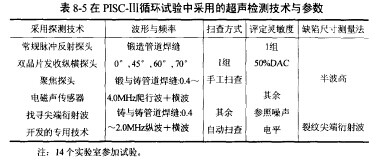
在循环试验中,各参加者采用自己的技术针对各种不锈钢管道焊缝的晶间应力腐蚀裂纹、疲劳裂纹及其它各类人工置入的缺陷进行超声检测可靠性的研究。在此基础上参照ASME-XI卷中的规定,对每种技术检测结果所得出的缺陷检出率、伪缺陷信号出现率、缺陷尺寸测量误差等进行对比,从而可评定各种检测技术的可靠性与有效性。摘要结果见表8-6,
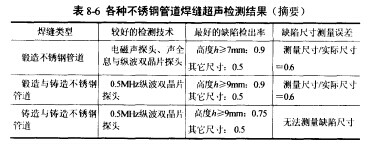
细节分述如下:
一、锻造不锈钢管道焊缝 1)不同检测技术取得的缺陷检出率与伪缺陷信号出现率如图8-8所示,
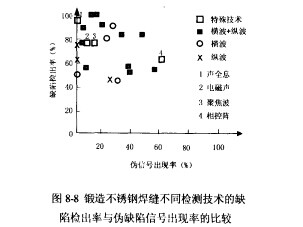
从图中以看出:
· 电磁声探头水平极化横波与声全息探伤的伪缺陷信号和噪声干扰较低,检测效果较好。
· 超声横波检测晶间应力腐蚀裂纹最灵敏(位于热影响区),但是伪缺陷信号很多,噪声较高,容易影响检测结果。
· 2MHz的纵波聚焦探头检出效果好,其伪信号少且噪声低。双晶片发射与接收分离的纵波准聚焦探头效果更好。
· 测量表面裂纹尺寸的关键是找到端点信号,如果能发现端点信号,测量会很准确。
2)14个参加循环试验的实验室中有—半达到缺陷检出率75%。当缺陷自身高度大于7mm时,其检出率可高达90%。难检的缺陷顺序为:多叉的晶间应力腐蚀裂纹,轴向晶间应力腐蚀裂纹与奥氏体焊缝内的光滑缺口。
3)缺陷高度与长度测量误差很大,数据分散,测量长度属实际长度之比的约为0.6(理想为1)。
二、锻造与铸造、铸造与铸造不锈钢管间的焊缝 1)低频(0.5MHz)纵波对奥氏焊缝探伤有利。共中双晶片纵波准聚焦探头的焦在30mm以内时,可以较好地探测近表面缺陷,在50~60mm范围时,可获得较好的缺陷检出率。
2)电磁声探头对铸造奥氏体钢焊缝的检测并没有显示出明显的优点。
3)当缺陷高度大于壁厚的10%时检出率较好,65%的参加者能检出这类缺陷。其它缺陷检出率较低,如A类疲劳裂纹、边界未熔合等的检出率仅为50%。而缺陷的正确判废率仅为75%。
4)锻-铸不锈钢管间的焊缝,辨认伪缺陷信号较容易,多数的参加组都能正确分辩出伪缺陷。在全铸造不锈钢管间的焊缝中存在大量的伪缺陷信号。例如,在133个伪缺陷信号中52处已达到不合格缺陷的水平。
5)在锻-铸不锈钢管焊缝缺陷尺寸的测量中,测量高度与实际高度之比小于0.6,测量长度与实际长度之比的可达0.7。
在全铸造不锈钢管焊缝超声检测中,缺陷长度和高度的测量结果都达不到要求。
总之,在堆焊、锻造和铸造不锈钢管的焊缝排序间,超声检测的难度也依次增加,见图8-9。
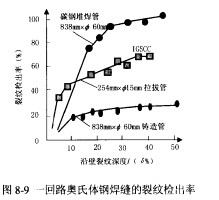
目前,不锈钢管道的焊缝,特别是壁厚较大的铸造不锈钢管焊缝其超声检测技术尚未彻庆解决。未来需要寻求更有效的技术来克服这类
不锈钢工程施工上焊缝检测的困难。